The Sensor Revolution: Achieving Unprecedented Quality Control in Bottle Wrapping
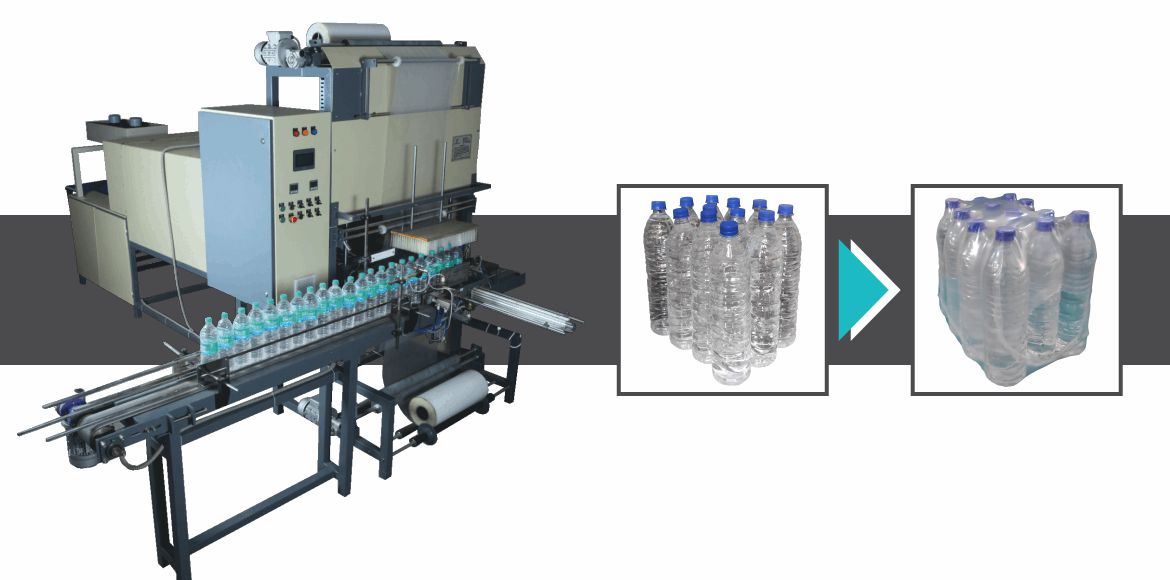
In the fast-paced world of consumer goods, packaging isn’t just a container; it’s a crucial part of the product experience, brand identity, and supply chain integrity. Bottles, whether holding beverages, pharmaceuticals, or household chemicals, often require secondary packaging – typically shrink wrapping – to create stable, marketable multipacks. For decades, ensuring the quality of this wrap relied heavily on operator experience and periodic manual checks. However, inconsistencies could lead to damaged products, retailer rejection, and tarnished brand reputation. Today, we’re witnessing a technological shift: a “sensory overload” in the best possible way, as smart sensors embed themselves into wrapping machinery, transforming quality control from a reactive measure into a proactive, data-driven science.
The Bottle Wrapping Machine is the mainstay of this procedure. These sophisticated pieces of equipment automate the application of film around a group of bottles, often followed by heat application (in the case of shrink wrapping) to create a tight, secure unit. Their fundamental purpose is efficiency and consistency, replacing manual labor and providing a uniform pack appearance. However, the mechanical precision of the machine is only one part of the equation. Achieving consistently perfect wraps – free from tears, loose film, crushed bottles, or poor seals – under varying conditions (film batches, ambient temperature changes, minor bottle variations) requires a layer of intelligence that goes beyond simple automation. This is where the power of integrated smart sensor technology truly shines, turning a standard wrapping machine into a vigilant quality guardian.
Modern manufacturing across diverse sectors leverages sensor technology to guarantee precision and safety. Consider, for example, the critical process parameters monitored in an HDPE Pipe Coupler Welding Machine. Sensors tracking temperature, pressure, and heating time are non-negotiable for ensuring a leak-proof, structurally sound weld vital for infrastructure integrity. Similarly, in bottle wrapping, specific sensors target critical quality parameters. Film tension sensors, for instance, are paramount. Too much tension can crush lightweight bottles or distort the pack; too little results in loose, sloppy wraps prone to shifting and tearing during transit. Smart tension sensors continuously monitor the force applied to the film, allowing the machine to make micro-adjustments in real-time, compensating for film inconsistencies or varying pack dynamics, ensuring optimal containment force without compromising product integrity.
Temperature control is another critical area, especially for shrink wrapping. Achieving the perfect shrink requires precise heat application – enough to shrink the film tightly but not so much that it burns through or weakens the material. Infrared temperature sensors or thermocouples placed strategically within the heat tunnel monitor the surface temperature of the film and the ambient tunnel temperature. This data allows the machine to dynamically adjust heating element output or conveyor speed, ensuring consistent results regardless of external factors. Furthermore, seal integrity sensors are becoming increasingly common. Ultrasonic sensors can detect microscopic flaws or incomplete seals along the film edges, preventing potential contamination or pack failure downstream. While the initial Shrink Wrapping Machine Price for a unit equipped with such advanced sensor arrays might be higher than a basic model, the return on investment is significant. The cost savings from drastically reduced product damage, packaging waste, customer complaints, and potential recalls far outweigh the upfront investment, proving that intelligent quality control is not a luxury but a sound financial decision.
Beyond physical parameters, machine vision systems act as powerful optical sensors, adding another layer of quality assurance. High-resolution cameras integrated into the wrapping line can perform a multitude of checks at high speed. They can verify the correct number of bottles in each pack, ensure proper bottle orientation, detect film tears or punctures invisible to simpler sensors, check for correct label placement (if visible through the wrap), and confirm the overall integrity and desired appearance of the finished multipack. These vision systems operate far faster and more reliably than human inspectors, flagging non-conforming packs for rejection or rework instantaneously, preventing flawed products from ever reaching the customer.
This “sensory overload,” however, is truly innovative not only in terms of detection but also in terms of the data produced. Each sensor – tension, temperature, ultrasonic, vision – is constantly collecting data points. This wealth of information is no longer isolated; it’s fed into the machine’s Programmable Logic Controller (PLC) and often transmitted to higher-level Manufacturing Execution Systems (MES) or Enterprise Resource Planning (ERP) software. This data stream enables powerful capabilities: real-time process adjustments to maintain quality, historical trend analysis to identify patterns or predict potential issues (predictive maintenance), optimization of machine settings for different products or films, and comprehensive quality reporting for traceability and compliance. Operators gain insights into machine performance previously unavailable, allowing for data-backed decision-making rather than guesswork.
This integration of sensor data aligns perfectly with the principles of Industry 4.0 and the Smart Factory. Bottle wrapping machines are no longer isolated units but connected nodes within a larger digital ecosystem. This connectivity allows for remote monitoring of machine status and quality parameters, facilitating faster troubleshooting and potentially reducing downtime. Maintenance teams can receive alerts based on sensor readings (e.g., abnormal motor vibration, inconsistent heating element temperatures) before a failure occurs, scheduling preventive action during planned downtime rather than suffering costly emergency breakdowns.
Of course, a true “sensory overload” could be counterproductive if the information isn’t presented effectively. Modern Human-Machine Interfaces (HMIs) play a crucial role in translating complex sensor data into intuitive dashboards and actionable alerts. Operators don’t need to be data scientists; they need clear indicators of system health, quality status, and specific guidance if an issue arises. Well-designed systems filter the noise, highlight critical information, and make it easy for personnel to understand what the sensors are telling them and what, if any, action is required. The goal isn’t to overwhelm but to empower operators with unprecedented insight and control over the wrapping process.
The quality control of bottle wrap is undergoing a significant transformation due to the use of smart sensors. Moving far beyond basic mechanical operation, modern wrapping systems equipped with an array of intelligent sensors offer unparalleled levels of precision, consistency, and insight. From ensuring optimal film tension and precise shrink temperatures to visually inspecting finished packs and detecting minuscule seal flaws, these technologies act as tireless guardians of quality. The data they generate fuels process optimization, predictive maintenance, and seamless integration into smart manufacturing environments. While the initial investment might be a consideration, the long-term benefits – reduced waste, minimized product damage, enhanced brand protection, improved efficiency, and valuable data insights – deliver a compelling return. For businesses seeking to achieve flawless packaging and optimize their end-of-line operations, embracing this sensor revolution is no longer optional; it’s essential. Partnering with experts like Innovative WrapTech Pvt. Ltd. can help businesses navigate these advancements, selecting and implementing the right sensor-driven solutions to meet their specific quality control needs and unlock new levels of packaging excellence.