Code Red to Green: How Smart Factories and Real-Time Data are Rewriting Pallet Wrapper Manufacturing
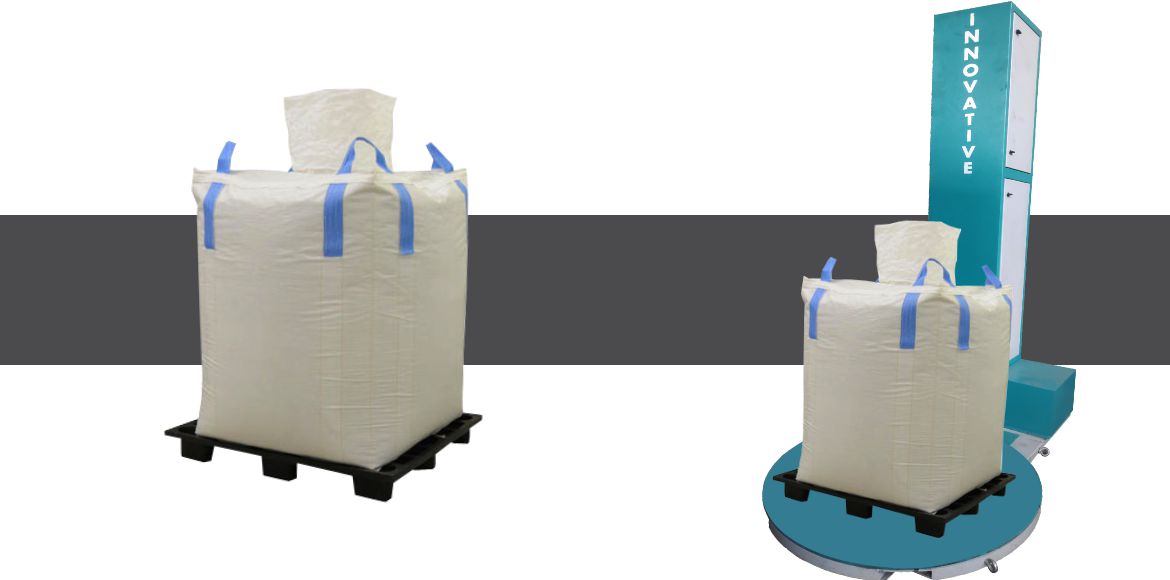
The manufacturing landscape is undergoing a seismic shift, propelled by the convergence of the Internet of Things (IoT), data analytics, and artificial intelligence (AI). This evolution, often dubbed Industry 4.0, is giving rise to “smart factories” – intelligent, interconnected facilities that operate with unparalleled efficiency, agility, and responsiveness. In this digitally-driven era, even seemingly conventional sectors like pallet wrapper manufacturing are experiencing a profound transformation. This allows companies to create a better product while also operating with greater safety and reliability.
Smart factories leverage a network of sensors, connected devices, and sophisticated software platforms to collect and analyze vast quantities of real-time data from every facet of the manufacturing process. From machine performance metrics and material consumption rates to environmental conditions and operator activities, this data provides invaluable insights that drive informed decision-making, optimize operations, enhance quality control, and proactively predict maintenance needs. This is especially important because manufacturing often involves heavy materials and high heat, which can quickly become dangerous. The combination of all these elements creates a safer and more effective operation.
One area where this has had an especially large impact is with Pallet Wrapping Machine Manufacture. By embedding sensors throughout the production line, manufacturers can monitor critical parameters such as welding temperatures, motor vibration, and electrical current draw. This data is then fed into analytics dashboards that provide real-time visibility into the health and performance of each machine component. For instance, if the temperature of a welding robot’s arm exceeds a predefined threshold, an alert can be automatically triggered, prompting technicians to investigate the issue before it leads to a costly breakdown. With this kind of monitoring, it’s now possible to perform actions that would have been science fiction in the past.
Another innovation that relies on these techniques is with Fully Auto Pallet Wrapping Machine. These machines now use data and sensors to optimize their performance more than ever before. These automated systems can analyze the shape, size, and weight distribution of the load being wrapped and automatically adjust wrapping parameters such as film tension, overlap, and number of wraps to ensure optimal security and stability while minimizing film usage. Data from previous wrapping cycles can be used to further refine these parameters, continuously improving efficiency and reducing waste. This reduces both environmental impact and overhead.
The benefits of these technologies can also be realized through the increased use of the Jumbo Bag Packing Machine. The combination of these machines and IoT devices allows for better integration and automation of the manufacturing process. For example, sensors can monitor the weight and dimensions of each bag as it’s being filled, ensuring consistent product quality and preventing overfilling or underfilling. Real-time data on material flow and machine performance can be used to optimize production schedules and minimize downtime, increasing overall throughput. They also make it easier to spot problems when they occur.
Beyond optimizing internal processes, smart factories also enable manufacturers to offer enhanced services to their customers. Remote monitoring capabilities allow manufacturers to track the performance of their machines in real-time, identify potential issues, and provide proactive maintenance and support. Predictive maintenance algorithms can analyze data from sensors and historical maintenance records to forecast when a machine component is likely to fail, enabling scheduled maintenance activities that prevent unplanned downtime and maximize machine uptime. This translates to improved customer satisfaction and stronger long-term relationships, which is the ultimate key to success.
Implementing smart factory technologies requires a strategic roadmap and careful consideration. Manufacturers must invest in the necessary infrastructure, including sensors, data acquisition systems, analytics platforms, and secure network connectivity. They also need to train their workforce to effectively use and interpret the data generated by these systems. Data security is paramount, and robust cybersecurity measures must be implemented to protect sensitive data from unauthorized access and cyberattacks. However, the long-term benefits of smart factory adoption far outweigh the initial investment and challenges.
The shift towards smart factories is not just a technological trend; it represents a fundamental shift in the way manufacturing is conducted. Companies that embrace these technologies will gain a significant competitive advantage, enabling them to produce higher-quality products more efficiently, respond quickly to changing customer demands, and achieve new levels of operational excellence. This transition can be challenging, but the rewards will be well worth it.
In conclusion, the integration of IoT, data analytics, and AI is transforming the landscape of pallet wrapper manufacturing and other industrial sectors. By embracing smart factory principles, manufacturers can unlock new levels of efficiency, sustainability, and customer satisfaction. Innovative WrapTech Pvt. Ltd. is dedicated to remaining at the forefront of this revolution by developing innovative and connected solutions that help our customers thrive in the era of Industry 4.0. We believe that the future of manufacturing is smart, data-driven, and customer-centric, and we are committed to helping our clients realize that future.