Decoding the Wrap: An Infographic Guide to Understanding Your Semi-Automatic Pallet Wrapper
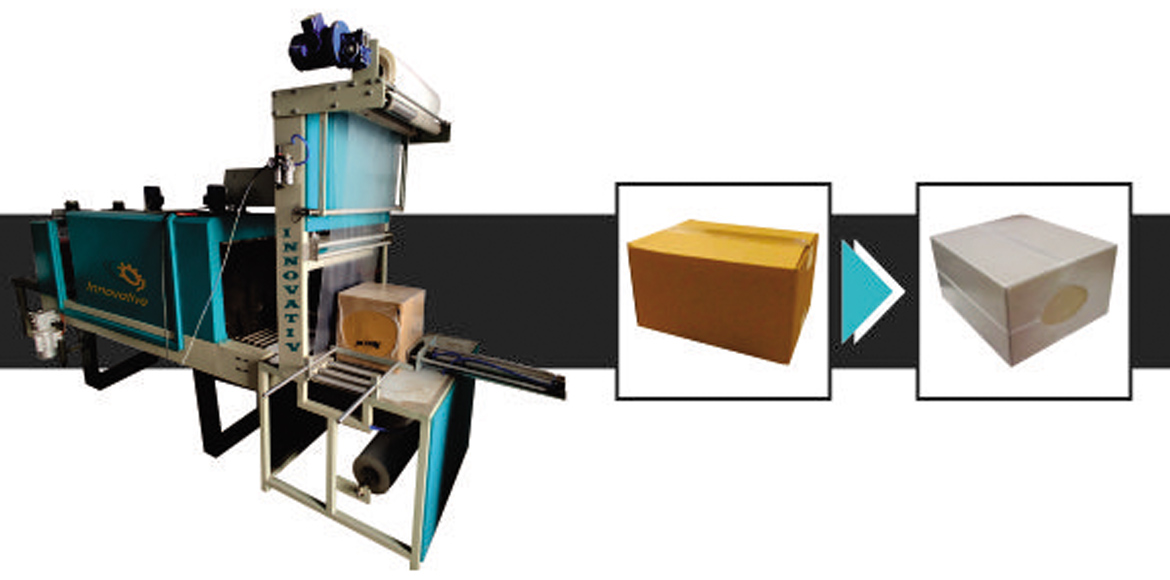
Pallet wrapping machines are workhorses in countless industries, ensuring the safe and secure transport of goods. But behind the seemingly simple process of applying stretch film, lies a carefully engineered piece of machinery. Today, we’re diving deep into the anatomy of a Semi Automatic Pallet Wrapper Machine, breaking down its key components and explaining how each part contributes to its overall effectiveness. This blog post will serve as an infographic guide, explaining the machine visually and providing detailed explanations for each component. Instead of simply telling you that it’s useful, this guide will provide a detailed look at exactly what makes these machines so vital.
The foundation of any Semi Automatic Pallet Wrapper Machine is its robust base or chassis. This solid platform provides stability during the wrapping process and houses essential components like the control panel and the motor drive. Typically, the base is made of heavy-duty steel, ensuring the machine can handle the weight of large pallets without vibrations or instability. A reliable base is critical for maintaining the machine’s integrity and its ability to consistently wrap pallets effectively. This initial section of the machine provides the grounding and structure for the entire operation. Without it, the precise movement and wrapping tension would be impossible. Directly attached is the turntable, a key part of the machine that rotates the pallet during the wrapping cycle, allowing the film to be applied evenly across all sides of the load. This turntable’s speed and rotation can be controlled to ensure optimal wrapping. This brings us to the next crucial element, the film carriage. Unlike a Shrink Wrapping Machine Manufacturer, who deals with heat and specialized films, the stretch wrapping machine’s film carriage manages the application of stretch film.
The stretch film must be held and dispensed by the film carriage. It moves up and down the mast (vertical support structure) as the pallet rotates, enabling the film to be applied uniformly from the base to the top of the pallet. The film carriage usually incorporates a tension control system, which allows the operator to adjust the amount of tension applied to the film. This ensures the load is tightly secured without the risk of the film breaking or causing damage to the products. This tensioning mechanism is a vital component, ensuring the film tightly binds the package while avoiding ripping. The film itself is a core factor in the wrapping process, and there is variety of film types and gauges available, each chosen based on the load’s specific needs. The film carriage, therefore, is not a simple dispensing mechanism but is an important part of what makes each individual wrap effective. Moreover, the mast’s role in the process is critical. The mast, or vertical support, is the structure that supports the film carriage and allows it to move up and down during the wrapping cycle. It’s usually made of steel and it’s designed to withstand the stress exerted by the carriage as it travels. An Automatic L-Sealer Machine has a different construction as it uses heat to seal a film, and the mast in a stretch wrapping machine primarily provides the vertical guidance that determines the path of the film around the pallet.
The control panel, another vital element of a semi-automatic machine, allows operators to program and control the wrapping cycle. It offers options for adjusting the number of turns, turntable speed, film tension, and number of wraps applied to the pallet’s top and bottom. The control panel can be basic with simple push-button controls or more advanced with digital displays and more sophisticated programmable options depending on the machine model. Through this panel, an operator can also adjust the settings based on the type of load being wrapped. For instance, the machine requires a softer setting if the product is light or extremely delicate. Conversely, for heavy or less delicate products, stronger settings might be necessary. The ability to customize the wrapping process is a critical element of a semi-automatic machine’s usability and effectiveness. Also crucial is the pre-stretch system, often found in more advanced semi-automatic models. This mechanism stretches the film before it is applied to the load, maximizing film usage and reducing costs. By stretching the film, it becomes thinner, allowing a larger area to be wrapped per film roll and providing improved load securing strength.
Finally, safety features are key in any pallet wrapping machine. Emergency stop buttons are a must, along with guarding or safety barriers to prevent accidental contact with moving parts. These safety measures are vital for the operator and anyone in the immediate vicinity of the machine, promoting workplace safety and compliance. These machines can move quite quickly when wrapping, and the safety elements help prevent accidental injury or contact with parts of the machine. Also, some machines also have warning lights and sounds that will alert nearby workers that the machine is in operation. This combination of physical safety and visual and audible alerts make the semi-automatic pallet wrapping machine an efficient and safer option than manual wrapping processes.
The components discussed work together to provide consistent, reliable, and safe pallet wrapping. Each part has its defined purpose, and combined, these components make these machines efficient workhorses in any warehouse or manufacturing setting. The infographic representation is designed to help users understand the functions of each component and, by extension, learn the functionality of the semi-automatic machine.
Understanding the anatomy of your Semi Automatic Pallet Wrapper Machine empowers you to maximize its effectiveness and ensure consistent performance. From the robust base and rotating turntable to the precision of the film carriage and control panel. At Innovative WrapTech Pvt. Ltd., we’re dedicated to providing top-quality wrapping solutions and supporting our clients in achieving optimal efficiency. The understanding of your machine helps you make more informed choices about maintenance and operation, contributing to increased efficiency and longevity of your machine.