From Chaos to Containment: Banishing Pallet Wrap Nightmares with Precision Settings
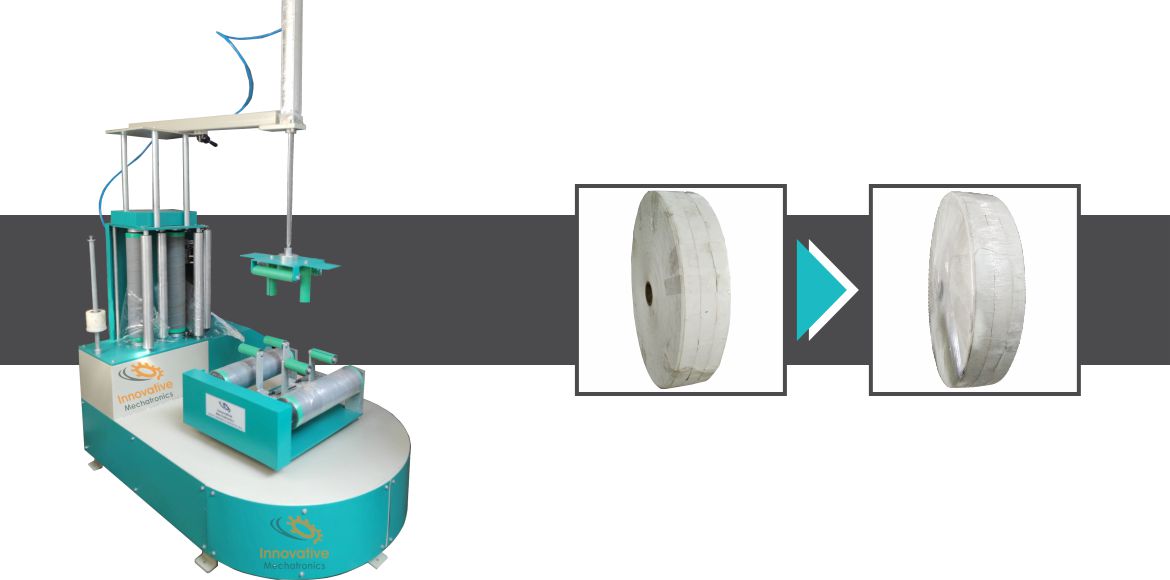
Securely wrapped pallets are a silent testament to efficiency and care in the world of warehousing and logistics. It represents products safely contained, ready for transit, and likely to arrive at their destination intact. On the other hand, a pallet that is not properly wrapped is a “wrapping nightmare” that is about to explode. Load shifts during transport, crushed boxes, torn film leading to contamination or pilferage, and even complete pallet failure are all costly consequences. These nightmares result in damaged goods, rejected shipments, safety hazards for handlers, wasted materials, lost time, and ultimately, damage to your bottom line and reputation. While factors like pallet quality and load configuration play a role, the most common culprit behind these failures often lies hidden in plain sight: incorrect settings on the very machine designed to prevent them.
The hero (or potential villain) in this scenario is the Pallet Wrapping Machine. Whether it’s a turntable, rotary arm, or robotic system, its fundamental job is to apply stretch film consistently and efficiently around a load, unitizing it for stability and protection. These machines offer significant advantages over manual wrapping in terms of speed, consistency, and film economy. However, owning one is only half the battle. Simply turning it on and letting it run with factory defaults or settings used for a completely different product is a recipe for disaster. The true power of these machines lies in their adjustability, allowing users to fine-tune the wrapping process to the specific needs of each load, transforming potential chaos into reliable containment. Understanding and mastering these settings is the key to banishing wrapping nightmares for good.
One of the most frequent and dangerous failures is load shifting, where layers or individual items move during handling or transit, compromising the pallet’s integrity. The squeezing pressure the film applies to the load, known as containment force, is frequently the cause of this. The base is where the proper containment force is first achieved. Many advanced systems offer features like Bottom Roll Packing with Holding System capabilities, ensuring the film is effectively ‘locked’ to the pallet itself. This prevents the entire load from sliding off its base, a common and catastrophic failure mode. Key machine settings here include the bottom wrap count (typically 3-5 wraps minimum to secure the load to the pallet) and film tension or wrap force. Insufficient tension results in a loose wrap that offers little support, while the number of bottom wraps dictates how securely that initial foundation is laid. Furthermore, the pre-stretch percentage (how much the film is elongated before application) directly impacts the film’s holding power and economy – maximizing pre-stretch appropriate for the film type ensures optimal performance and reduces material cost.
Another common nightmare is film puncture or tearing during or after the wrapping cycle. This exposes the product to dirt, moisture, and potential tampering or damage. Sharp corners on boxes, protrusions from the load, or simply snagging during handling can initiate a tear. While robust film selection is important, machine settings play a critical role. Sourcing equipment from a reputable Plastic wrapping Machine Manufacture often means better design features that minimize snag points and ensure smoother film delivery. Settings-wise, excessive film tension or pre-stretch can thin the film too much, making it susceptible to breaking on corners. Reducing the tension slightly, especially during the initial wrap phase, can help. The film carriage ascent/descent speed also matters; moving too quickly around sharp corners increases the stress on the film. Some machines offer a “film roping” feature, where the film is gathered into a rope-like band at the top and/or bottom, reinforcing these critical areas against tearing, albeit sacrificing some surface coverage. Adjusting the overlap between film layers (controlled by carriage speed relative to rotation speed) also ensures adequate coverage and strength.
Product crushing is the devastating consequence of applying too much containment force, particularly with fragile goods, light corrugated boxes, or compressible products. It’s easy to assume “tighter is always better,” but this can lead directly to unsaleable goods. The primary culprit here is excessive film tension or wrap force. Modern machines allow precise control over this parameter, enabling operators to dial down the force for delicate loads. If the machine is equipped with a top platen or pressure system (used to stabilize light or unstable loads during wrapping), the top platen pressure itself must be adjusted carefully to avoid crushing the top layers. Tailoring the number of wraps applied (top wrap count and overall wrap program) is also crucial – applying fewer layers of film inherently reduces the cumulative compressive force on the load.
Film tailing, where the end of the film isn’t properly secured and drags or flaps loosely, might seem like a minor annoyance, but it can be a significant problem. Loose tails can get caught in conveyor systems, forklifts, or automated storage and retrieval systems (AS/RS), potentially causing jams, damaging equipment, or even pulling the wrap apart. This nightmare usually points to issues with the machine’s cut and wipe system (or heat seal system). Settings related to the timing, pressure, and duration of the clamp, cut, and wipe/seal mechanism need to be correctly adjusted for the specific film type and thickness being used. Worn-out wiping brushes, dull cutting blades, or misaligned clamping pads are common maintenance issues that manifest as film tails, highlighting the interplay between correct settings and proper machine upkeep.
Crucially, preventing these nightmares requires acknowledging that not all loads are created equal. A pallet of heavy, uniform boxes requires vastly different settings than a pallet of lightweight, irregularly shaped containers or fragile bottles. This is where load profile awareness and machine flexibility become vital. Operators must understand the characteristics of the load – its weight, stability, shape, and fragility – and adjust settings accordingly. Modern pallet wrappers often feature programmable controllers (PLCs) with recipe storage. This allows operators to save optimized settings for specific product types, ensuring consistent, repeatable, and correct wrapping parameters are applied every time with minimal manual input, reducing the risk of human error.
The type of stretch film used also profoundly impacts the effectiveness of machine settings. Films vary in gauge (thickness), puncture resistance, cling, and maximum pre-stretch capability. Applying settings designed for a high-performance, high-stretch film to a lower-grade conventional film will likely result in film breaks and inadequate containment. Conversely, under-stretching a high-performance film wastes its potential and increases costs. Machine settings must be calibrated to match the specifications and capabilities of the film being run to achieve optimal results and avoid failures.
Finally, even the most advanced machine with perfectly dialed-in settings is ineffective without proper operator training and regular preventative maintenance. Operators need to understand why certain settings are important, how to make adjustments correctly, how to load film properly, and how to identify early signs of potential problems. Regular maintenance ensures that components like rollers, grippers, cutters, and sensors are functioning correctly, allowing the machine settings to translate into reliable, real-world performance.
Pallet wrapping nightmares – from shifted loads and torn film to crushed products and trailing ends – are largely preventable. The key lies in moving beyond a “set it and forget it” mentality and embracing the precision control offered by modern pallet wrapping machines. By carefully considering the load profile, selecting the appropriate film, and meticulously adjusting machine settings like wrap force, pre-stretch, wrap counts, and cut/wipe parameters, businesses can dramatically improve load security and reduce costly failures. Understanding how these settings interact and investing in operator training and machine maintenance closes the loop, ensuring consistent and reliable performance. Companies like Innovative WrapTech Pvt. Ltd. specialize in providing not only robust wrapping equipment but also the expertise to help businesses optimize their settings, troubleshoot issues, and ultimately transform potential wrapping chaos into secure, dependable containment, protecting products, profits, and peace of mind.