One Arm, Many Talents: Integrated Functions in Robotic Pallet Wrapping
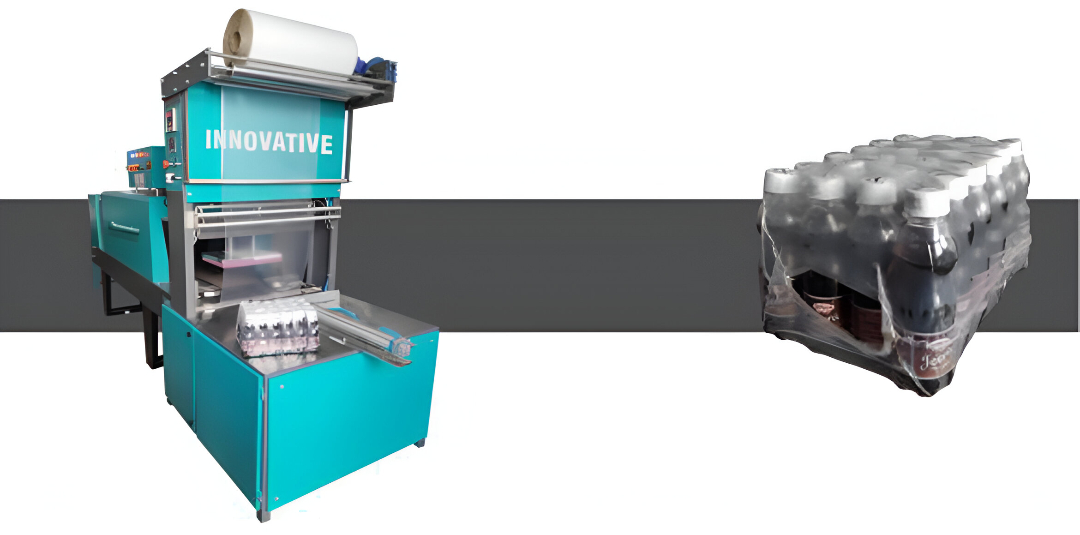
The relentless drive for efficiency in modern warehousing and logistics operations constantly pushes automation boundaries. End-of-line packaging, the final stage before goods embark on their journey, is a prime area for optimization. Traditionally, tasks like palletizing, wrapping, applying top sheets, and labeling often required separate machines, each occupying valuable floor space, demanding individual integration, and creating potential bottlenecks during transfers. However, the rise of robotics is ushering in an era of consolidation, where a single robotic system can intelligently perform multiple tasks. Nowhere is this trend more impactful than in pallet wrapping, where robots are evolving beyond simple film application to become multi-talented workhorses integrating crucial functions like labeling and top sheet dispensing.
The core enabling technology for this evolution is the Robotics Pallet Wrapper machine. Robotic wraps use a multi-axis (usually 6-axis) industrial robot arm, as opposed to conventional turntable or rotary arm wrappers, which function inside a fixed mechanical framework. This innate adaptability provides an unmatched range of motion. The robot can accurately place its end-of-arm tooling (EOAT) wherever in its work envelope, so it’s not limited to just circling a pallet. This fundamental difference unlocks the potential to perform tasks beyond just dispensing stretch film. It can reach over the top of the load, precisely target specific faces or corners, and interact with peripheral equipment like label printers or sheet dispensers in ways fixed automation simply cannot replicate. This flexibility turns the wrapping station into a multipurpose packing cell rather than a single-purpose device.
This capability stands in stark contrast to simpler forms of automation. Consider the Semi Automatic Pallet Wrapper Machine. These units typically require an operator to manually attach the film tail, initiate the wrap cycle, and cut the film at the end. While they significantly improve consistency and reduce manual labor compared to hand wrapping, their mechanical design is inherently limited. They lack the sophisticated control systems, sensors, and dexterity needed to pick up a label, align it accurately, and apply it, or to grasp and position a large top sheet. Integrating such functions into a semi-automatic machine would be impractical and negate its primary advantage of relative simplicity and lower cost. The leap from semi-automatic to robotic wrapping isn’t just about removing the operator further from the process; it’s about introducing a level of intelligence and physical dexterity that enables true task consolidation.
Similarly, while other automated packaging machines handle related tasks, they typically lack the inherent flexibility for this type of integration. A Shrink Wrapping Machine, for instance, excels at creating tightly sealed packs using heat-shrinkable film, often employed for bundling individual products or creating fully enclosed pallet loads for weather protection. While labeling or top sheeting might occur before or after the shrink process in the overall line, the shrink machine itself (whether a tunnel or ring design) is highly specialized for film application and heat treatment. Its core function and mechanical structure don’t lend themselves to easily incorporating precise label application or top sheet handling within its own operational cycle. The unique advantage of the robotic wrapper lies in the robot arm’s versatility, allowing it to seamlessly switch between film dispensing and other tasks using specialized EOAT within a single operational footprint.
Integrating Labeling:
One of the most valuable integrated functions is automated label application. In a robotic cell, this often involves a print-and-apply (LPA) system positioned within the robot’s reach. The sequence might look like this:
- The pallet arrives at the wrapping station.
- The robot performs the primary wrap cycle.
- Towards the end or after the wrap, the robot moves its specialized EOAT (which might include vacuum cups or grippers alongside the film dispenser, or utilize a tool changer) to the LPA unit.
- The LPA prints the required label (often containing SSCC barcodes, shipping info, lot codes).
- The robot takes the printed label and precisely applies it to the designated location(s) on the wrapped pallet – side, top, or even corner-wrap application is possible with robotic dexterity.
The benefits are substantial:
- Accuracy: Robotic application eliminates human error in label placement, crucial for automated scanning downstream.
- Speed & Efficiency: Labeling occurs within the wrapping cycle or immediately after, eliminating transfer time to a separate labeling station.
- Footprint Reduction: One machine cell handles two tasks, saving valuable floor space.
- Simplified Control: Both wrapping and labeling parameters are managed through the integrated robotic system controller.
Integrating Top Sheet Application:
Protecting the top of the pallet from dust, moisture, or providing additional load stability is often achieved with a top sheet. Robots can automate this typically manual or separate machine step:
- A top sheet dispenser (holding a roll of film or pre-cut sheets) is located within the robot’s work envelope.
- Before or during the wrap cycle (often just before the final top wraps), the robot utilizes its EOAT (potentially changing tools if necessary) to grab the leading edge of the top sheet material.
- The robot extends the sheet over the top of the pallet load.
- The sheet is cut (by an integrated cutter on the dispenser or the robot’s EOAT).
- The robot then completes the wrap cycle, securing the top sheet edges with the final layers of stretch film.
The advantages mirror those of integrated labeling:
- Automation: Eliminates a manual task or the need for a separate top sheet dispensing machine.
- Protection: Ensures consistent and reliable top coverage.
- Integration: Seamlessly incorporates protection into the unitization process.
- Efficiency: Reduces overall cycle time compared to separate operations.
Technical Considerations and Challenges:
While the benefits are clear, designing an effective multi-tasking robotic cell requires careful consideration:
- End-of-Arm Tooling (EOAT): The EOAT is critical. It might be a complex, multi-function tool capable of handling film, labels, and top sheets, or the system might employ an automatic tool changer, allowing the robot to quickly swap between specialized tools. EOAT design directly impacts capability, speed, and cost.
- Cell Layout and Safety: Integrating additional equipment (LPA, top sheet dispenser) requires careful planning of the cell layout to ensure the robot has adequate reach without interference, while maintaining stringent safety standards with guarding, light curtains, or area scanners.
- Programming and Control: Programming the robot to perform multiple, intricate tasks sequentially or simultaneously requires expertise. The control system must manage the timing and coordination of all functions flawlessly.
- Cycle Time: While consolidating tasks saves transfer time, adding labeling or top sheeting inherently adds time to the overall wrapping station cycle. This needs to be factored into throughput calculations.
- Complexity and Maintenance: A multi-tasking robot cell is inherently more complex than a single-function machine, potentially requiring more specialized maintenance skills.
The end-of-line, single-task machine age is changing. Robotic pallet wrappers are demonstrating that one robotic arm can indeed possess many talents, effectively consolidating crucial tasks like stretch wrapping, label application, and top sheet dispensing into a single, efficient cell. While challenges exist in design and implementation, the benefits – reduced footprint, enhanced efficiency, improved accuracy, simplified integration, and greater flexibility – are compelling drivers for adoption. This consolidation represents a significant step towards more streamlined, adaptable, and autonomous end-of-line packaging operations. For businesses looking to leverage these advancements, partnering with specialists like Innovative WrapTech Pvt. Ltd., who understand the intricacies of robotic automation and integrated packaging solutions, is key to designing and implementing systems that deliver maximum value and performance, transforming end-of-line processes from a series of steps into a single, seamless operation.