The Tight Fit: Unveiling the Art of Film Tension Control in Automatic Shrink Wrapping
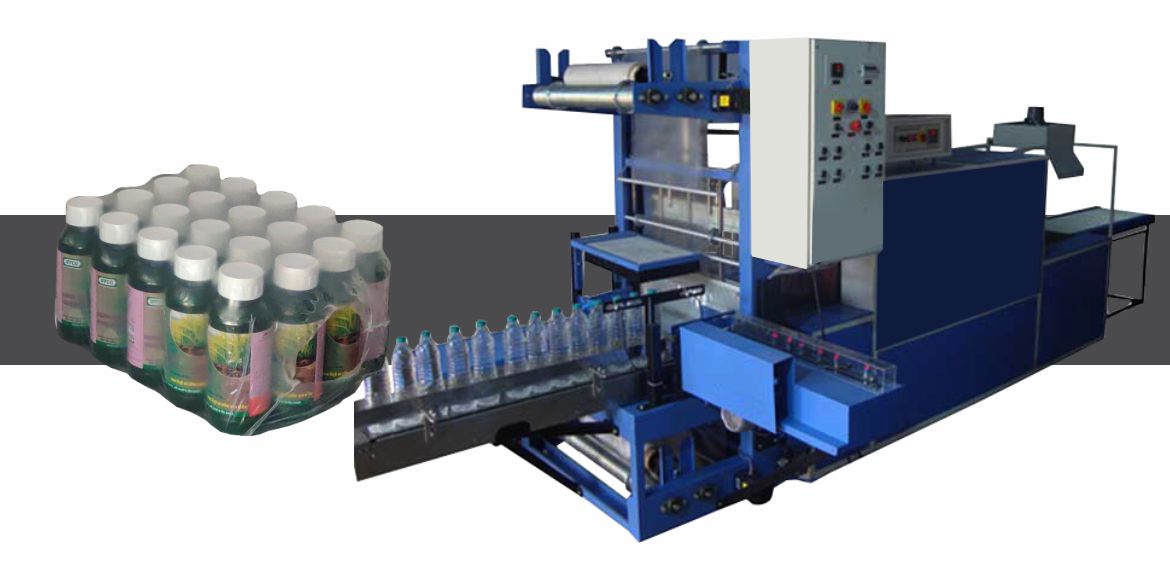
In the world of packaging, where presentation is often as important as protection, a flawlessly shrink-wrapped product speaks volumes. It conveys quality, professionalism, and attention to detail. But it takes more than just heat and plastic to create the ideal, wrinkle-free shrink wrap. It’s a delicate dance orchestrated by a critical element: film tension control. Without it, the dream of perfectly wrapped products quickly dissolves into a mess of puckers, creases, and unattractive imperfections.
The challenge lies in the nature of shrink film itself. It is a thin, flexible substance that, when heated, closely conforms to a product’s contours. However, this flexibility also makes it susceptible to stretching, tearing, and wrinkling if the tension is not carefully managed during the wrapping process. A fully automatic shrink-wrapping machine handles the complexities of this process, precisely metering the film, applying consistent tension, and ensuring uniform shrinkage for optimal results. A Fully Automatic Shrink Packing Machine is designed to do just that, by providing the right temperature and pressure it ensures that each products is wrapped safely and securely. With the rise of automation, the need for sophisticated tension control systems has become paramount. These systems monitor and adjust the tension of the film in real-time, compensating for variations in film thickness, product size, and machine speed.
One of the ways companies are able to reduce the cost and time it takes to wrap items is through the use of modern wrapping equipment. The most modern wrapping equipment provides a way to wrap items on the horizontal axis. Imagine trying to wrap a lengthy pipe or piece of lumber while on a production line and doing it without the help of an Horizontal Stretch Wrapping Machine. The use of this equipment saves you the labor time that you need in order to have those products wrapped. As packaging speeds increase and product lines become more diverse, precise film tension control becomes increasingly vital. These machines work by rotating the item while at the same time stretching and securing the film around the item.
The most amazing advancements are often created in order to solve very particular problems. Consider how you would wrap a very heavy piece of machinery or large auto part with shrink wrap. Typically, that would take a lot of labor and would not be consistent but you can solve all of those problems with a specifically built Tread Rubber Stretch Wrapping Machine. While the name says “tread rubber”, they can be used for more than just tires and are often a solution that companies use to quickly and consistently wrap their large items. As you can see, the proper film tension control prevents uneven shrinkage, which can lead to unsightly wrinkles or even tears in the film. It ensures that the film conforms smoothly to the product’s surface, creating a tight, secure, and visually appealing package.
The Science of Tension Control:
Effective film tension control involves a combination of mechanical design, sensor technology, and sophisticated control algorithms. Key components include:
- Film Unwind System: This system carefully dispenses the shrink film from the roll, maintaining consistent tension as the roll diameter decreases. Dancer rollers and feedback loops are often used to prevent sudden jerks or slack in the film.
- Tension Sensors: These sensors continuously monitor the tension of the film as it travels through the machine. They provide real-time feedback to the control system, allowing for precise adjustments.
- Braking Systems: Brakes are used to apply resistance to the film unwind, maintaining a consistent tension even as the machine speeds up or slows down.
- Servo Motors: Servo motors provide precise and responsive control over the film unwind and braking systems, allowing for minute adjustments to the film tension.
- Control Algorithms: Sophisticated algorithms analyze the data from the tension sensors and adjust the braking and servo motor settings to maintain the desired film tension. These algorithms can also compensate for variations in film properties and product dimensions.
The Impact of Poor Tension Control:
The consequences of inadequate film tension control can be significant:
- Wrinkled Wraps: Uneven tension leads to wrinkles and creases, detracting from the product’s appearance and potentially damaging the packaging.
- Loose Wraps: Insufficient tension results in loose, baggy wraps that offer inadequate protection and can shift during transit.
- Torn Film: Excessive tension can cause the film to tear, leading to product exposure and potential damage.
- Inconsistent Shrinkage: Uneven tension can result in inconsistent shrinkage, causing some areas of the wrap to be tighter than others.
- Increased Material Waste: When film tension is not properly managed, the risk of errors and damaged wraps increases, leading to higher material waste.
Applications Across Industries:
Film tension control is critical in a wide range of industries that rely on shrink wrapping, including:
- Food and Beverage: Ensuring that food products are tightly and securely wrapped to maintain freshness and prevent contamination.
- Pharmaceuticals: Protecting sensitive pharmaceutical products from moisture, light, and tampering.
- Consumer Goods: Enhancing the appearance and shelf appeal of consumer products, while also providing protection during shipping and handling.
- Industrial Goods: Securing and protecting industrial products, such as machinery parts and building materials.
- Printing and Packaging: Wrapping stacks of printed materials or bundled products for distribution.
Advancements and Future Trends:
The field of film tension control is constantly evolving, with new technologies and techniques being developed to improve the accuracy, reliability, and efficiency of shrink-wrapping processes. Some key trends include:
- Smart Sensors: The use of advanced sensors that can detect subtle variations in film thickness, temperature, and other parameters.
- Adaptive Algorithms: The development of adaptive algorithms that can learn and adjust to changing conditions in real-time.
- Remote Monitoring and Control: The ability to monitor and control film tension settings remotely, allowing for greater flexibility and efficiency.
- Integration with Automation Systems: Seamless integration of film tension control systems with other automation components, such as robotics and conveyors.
In conclusion, film tension control is the unsung hero of the shrink-wrapping process, ensuring that products are not only protected but also presented in the best possible light. With advanced sensors, intelligent algorithms, and sophisticated control systems, it’s now possible to achieve consistently perfect, wrinkle-free shrink wraps with fully automatic machines. At Innovative WrapTech Pvt. Ltd., we are dedicated to providing the best solutions for your wrapping needs and we understand the importance of the right type of film tension on all our equipment. We continuously innovate and improve our wrapping machines with the latest technology.