The Uptime Imperative: Your Daily & Weekly Ritual for a Flawless Pallet Wrap Cycle
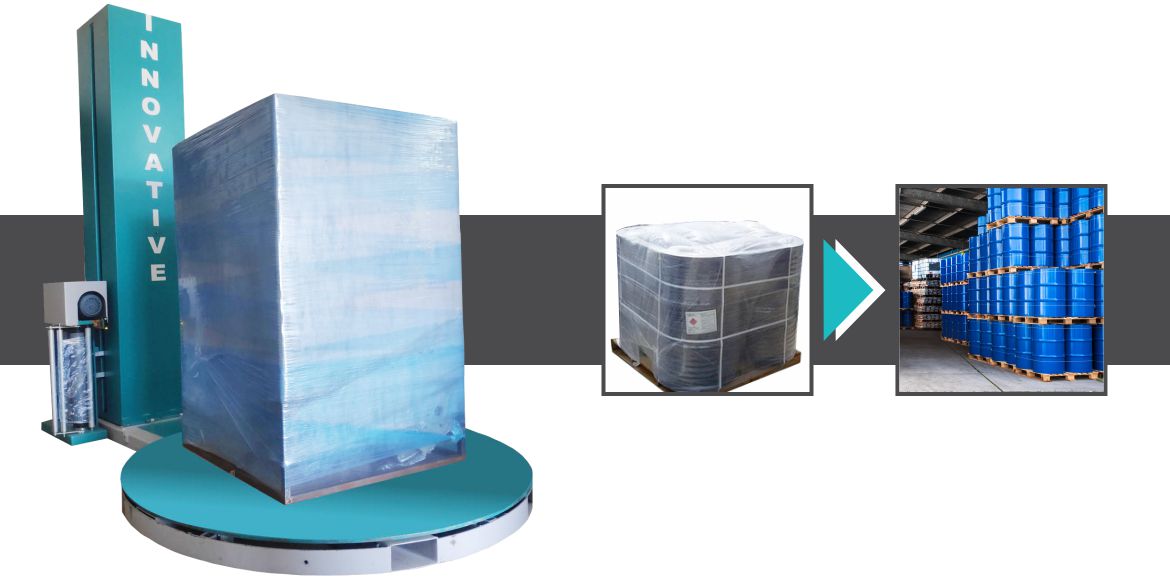
In the dynamic ecosystem of logistics and manufacturing, predictable output is paramount. Unplanned downtime isn’t just an inconvenience; it’s a direct hit to productivity, schedules, and ultimately, the bottom line. Your automatic pallet wrapper, diligently securing loads for safe transit, is a linchpin in this process. While often reliable, neglecting its basic needs is a gamble that rarely pays off. Stoppages mean delays, potential product damage during manual handling, and frustrated teams scrambling to catch up. The most effective strategy to sidestep these disruptions lies not in complex repairs, but in consistent, proactive care. This guide outlines a simple yet essential daily and weekly preventative maintenance (PM) checklist designed to keep your wrapper running smoothly, extend its operational life, and ensure every wrap is as good as the first.
Implementing a routine PM schedule is vital, especially considering the operational demands placed upon an Auto pallet Wrapper Machine. These units are more than just rotating platforms and film dispensers; they are integrated systems involving precise controls, sensors detecting load heights and positions, motors driving rotation and film carriage movement, and sophisticated mechanisms for stretching film effectively. The constant vibration, dust inherent in many warehouse environments, and the mechanical stresses of operation mean that components naturally wear over time. Regular checks allow you to spot and address minor issues – like accumulated debris interfering with a sensor, a loose fitting, or early signs of roller wear – before they cascade into significant malfunctions that bring your entire end-of-line process to a standstill, demanding costly emergency repairs and causing substantial delays.
From the viewpoint of a dedicated Plastic wrapping Machine Manufacture, the emphasis on preventative maintenance is rooted in ensuring customer success and equipment longevity. Manufacturers invest significantly in engineering robust, efficient, and safe machines. The maintenance schedules detailed in operational manuals are provided because they know, through extensive testing and field experience, what is required for the equipment to consistently meet its performance specifications – achieving optimal film economy through proper pre-stretch, maintaining consistent wrap tension for load security, and operating reliably shift after shift. Adhering to these manufacturer recommendations is not just about preventing breakdowns; it’s about maximizing the return on your investment, potentially fulfilling warranty requirements, and ensuring the machine operates at the peak efficiency intended by its designers, safeguarding both your product and your operational costs.
Furthermore, the reliability of your final wrap impacts the integrity of your entire production output, regardless of what processes precede it. Imagine a facility meticulously producing goods, perhaps utilizing high-capacity equipment like a Jumbo Bag Packing Machine to package bulk materials which are then palletized for shipment. All the effort, quality control, and resources invested upstream are jeopardized if the final pallet wrap is inconsistent or fails during handling or transport due to a poorly maintained wrapper. A compromised wrap can lead to load shifting, product damage, contamination, unsafe handling conditions, and potentially rejected shipments. Therefore, ensuring your pallet wrapper is in prime condition through regular PM is fundamental to protecting the value created earlier in your production line and maintaining the quality promise to your end customers.
Your Essential Preventative Maintenance Checklist
Make these checks a standard part of your operational workflow. Ensure operators are trained and understand the significance of each task. Consistency is the key to success.
Daily Checks (Perform Before Shift Start or During First Use – Approx. 5-10 Minutes):
- Visual Walk-Around & Area Safety:
- Action: Circle the machine. Look for any obvious signs of physical damage (dents, cracks, bent components), fluid leaks (check under motors/gearboxes), or loose/damaged wiring.
- Why: Catches potential hazards and prevents minor damage from worsening or causing operational failure. Leaks indicate seal or component issues needing attention.
- Action: Ensure the operating area is clear of obstructions: remove broken pallet wood, stray film, tools, banding, or any debris.
- Why: Prevents trip hazards, ensures safe operator movement, and stops debris from being pulled into moving parts, which can cause jams or damage.
- Film Roll & Dispensing System:
- Action: Verify the stretch film roll is correctly installed, securely clamped, and has sufficient material for upcoming runs. Verify that the film is correctly threaded through the film carriage’s whole roller system.
- Why: Incorrect loading or threading is a primary cause of film breaks, poor stretch, and inconsistent wrapping. Running out of film mid-cycle causes unnecessary delays.
- Action: Glance at the pre-stretch rollers (if applicable) and the dancer arm/bar. Look for any visible film fragments wrapped around them or significant residue build-up.
- Why: Inconsistent stretch percentages and possible film tearing result from film residue impairing roller grip and performance.
- Sensors & Photo-Eyes:
- Action: Inspect the lenses of the load height photo-eye and any safety sensors (light curtains, area scanners). Gently wipe with a clean, dry, soft cloth if dusty or smudged.
- Why: Clean, unobstructed sensors are critical for accurate operation (correct wrap height) and safety system integrity.Dirt or dust might lead to failures or erroneous readings.
- Safety Systems Check:
- Action: Confirm Emergency Stop buttons are easily accessible, clearly visible, and appear undamaged. Verify safety gates are closed and interlocks (if equipped) seem functional. Verify that the physical guards are firmly in position.
- Why: Ensures immediate shutdown capability in an emergency and that safeguards protecting operators from moving parts are operational. Safety is non-negotiable.
- Control Interface:
- Action: Upon powering up the machine, check the control panel or HMI screen for any displayed error codes, fault messages, or warning indicators.
- Why: Provides an early warning of potential electrical or system issues that may require troubleshooting before starting production.
- Listen for Anomalies (First Cycle):
- Action: Pay attention during the first wrap cycle. Listen for any unusual sounds – grinding, squealing, knocking, excessive vibration, or loud clicking.
- Why: Abnormal noises often indicate developing mechanical issues (e.g., worn bearings, loose chain, motor problems) that warrant further investigation.
Weekly Checks (Requires Proper Lockout/Tagout Procedure – Approx. 20-30 Minutes):
- Thorough Cleaning:
- Action: Safely power down and lock out/tag out the machine. Wipe down the entire film carriage assembly, rollers (especially pre-stretch rollers – use appropriate cleaner if needed per manual), mast, turntable surface or rotary arm structure, and frame. Use low-pressure compressed air (wear safety glasses!) cautiously to blow dust from motors, drive components, and control cabinet vents (check manual for warnings about sensitive areas).
- Why: Removes accumulated dust and grime that acts as an abrasive, accelerates wear, can interfere with sensors, and potentially cause overheating of electrical components.
- Film Carriage & Mast Inspection:
- Action: Inspect film carriage rollers closely for wear, scoring, or damage. If the carriage is being driven by belts or chains, check their tension and condition. Make sure the carriage travels along the mast smoothly and easily.
- Why: Film degradation and stretch are hampered by worn rollers. Proper drive tension and smooth movement are essential for consistent vertical wrap placement.
- Turntable / Rotary Arm Drive & Support:
- Action: Inspect the turntable drive chain/belt for proper tension (refer to manual specifications) and signs of wear, stretching, or damage. Check turntable support casters/bearings for smooth rotation and wear. For rotary arm models, inspect arm bearings and the main drive system similarly.
- Why: Ensures smooth, consistent rotation critical for uniform wrapping. Prevents jerky movements, excessive noise, and potential drive failure.
- Lubrication (Crucial – Follow Manual):
- Action: Consult the manufacturer’s manual for specific lubrication points, lubricant types (grease/oil specifications), and frequency. Apply the correct lubricant sparingly to designated points (e.g., chains, bearings, pivot points). Before using fresh grease, remove any old, filthy grease. Wipe away excess lubricant.
- Why: Avoids wear, distributes heat, lowers friction, and shields vital moving parts from corrosion.. Applying the incorrect kind or quantity of lubricant might be just as detrimental as not using any at all.
- Check Fasteners & Electrical Connections:
- Action: Visually inspect accessible nuts, bolts, and screws, particularly on motors, gearboxes, the mast base, and arm/turntable structures, ensuring they are snug. Check that visible electrical cables are secure, undamaged, and properly routed (not rubbing against moving parts).
- Why: Vibration can loosen fasteners over time, leading to misalignment or component failure. Secure electrical connections prevent intermittent faults.
- Review Key Parameters:
- Action: Briefly check the settings on the control panel for frequently used wrap programs (e.g., film tension, pre-stretch percentage, top/bottom wraps, rotation speed) to ensure they haven’t been unintentionally altered.
- Why: Guarantees consistency in wrap application according to established standards, preventing issues related to load stability or excessive film use.
Beyond the Tasks: Fostering a Maintenance Mindset
- Train & Empower: Ensure operators understand not just how to do the checks, but why they are important.
- Report Promptly: Create a culture where reporting small irregularities (odd noises, slight performance changes) is encouraged and acted upon quickly.
- Manual is Key: Always keep the machine-specific operational and maintenance manual accessible and treat it as the definitive guide.
- Keep a Log: Maintain a simple logbook to track when PM was performed, any issues noted, and corrective actions taken. This history aids troubleshooting.
- Professional Check-ups: Supplement these routine checks with scheduled professional maintenance by qualified technicians as recommended by the manufacturer for more in-depth inspections and adjustments.
Secure Your Operations with Proactive Care from Innovative WrapTech Pvt. Ltd.
Committing just a few minutes each day and a bit longer each week to the preventative maintenance of your automatic pallet wrapper is one of the highest ROI activities you can undertake in your facility. It transforms machine care from a reactive necessity into a proactive strategy, directly contributing to reduced downtime, consistent product protection, optimized material usage, enhanced safety, and a longer, more productive life for your equipment. At Innovative WrapTech Pvt. Ltd., we champion the value of reliable machinery and recognize that consistent, proactive maintenance is the bedrock upon which efficient and dependable packaging operations are built. Implement this routine, keep your wrapper spinning flawlessly, and secure the smooth flow of your business.